Importance of Regular Safety Feature Inspections
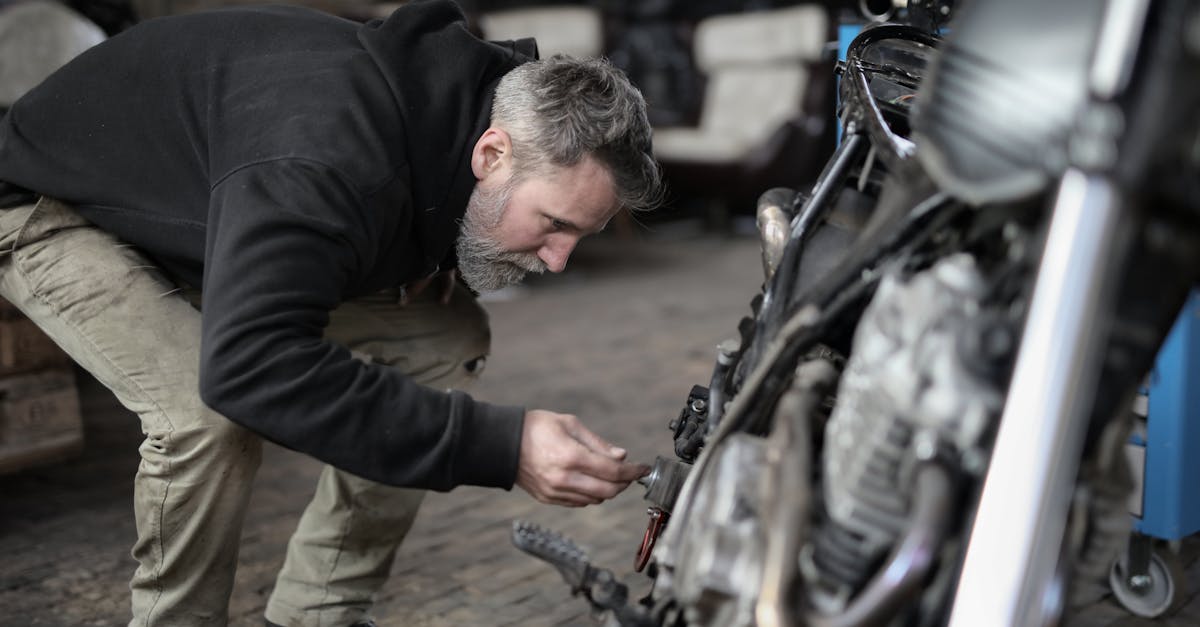
Table Of Contents
Common Issues Identified During Safety Feature Assessments
During safety feature assessments, various common issues are often identified that can jeopardize the overall safety of a workplace. One common issue uncovered during inspections is faulty emergency lighting systems. Emergency lighting plays a critical role during power outages or emergency situations, and any malfunction can pose a significant risk to occupants in the event of an evacuation.
Another prevalent issue observed during safety feature assessments is inadequate or poorly maintained fire suppression systems. Fire suppression systems are vital for quickly containing and extinguishing fires, safeguarding both lives and property. Failure to address maintenance issues with these systems can result in their inefficacy during a fire emergency, leading to potentially disastrous consequences.
Continue to read this blog post for more great tips.
Addressing Faulty Emergency Lighting Systems
Emergency lighting systems are crucial components of any workplace's safety measures, providing illumination in the event of power outages or emergencies. However, these systems can sometimes experience faults or malfunctions that compromise their effectiveness. When addressing faulty emergency lighting systems, it is essential to conduct regular inspections and maintenance to ensure their proper functioning when needed.
One common issue found in emergency lighting systems is dead batteries, which can render the lights useless during power failures. It is important to inspect and replace batteries as needed to guarantee that the emergency lights will activate when required. Additionally, regular testing of the entire emergency lighting system should be conducted to identify any deficiencies and address them promptly.
The Role of Qualified Professionals in Safety Inspections
Qualified professionals play a crucial role in ensuring the safety and wellbeing of individuals in a workplace. These professionals possess the expertise and knowledge required to conduct thorough safety inspections, identifying potential hazards and risks that may compromise the safety of employees. By entrusting safety inspections to qualified individuals, organizations can rest assured that all safety features and systems are in compliance with regulations and standards.
Certified safety inspectors are well-versed in the latest safety protocols and regulations, allowing them to provide accurate assessments and recommendations for enhancing workplace safety. Their training equips them to identify even the most subtle safety issues, enabling proactive measures to be implemented before potential incidents occur. Employing qualified safety professionals demonstrates a commitment to prioritizing the safety of personnel and the overall wellbeing of the workplace environment.
Importance of Hiring Certified Safety Inspectors
Certified safety inspectors play a vital role in ensuring workplace safety standards are met and maintained. Their expertise and training enable them to identify potential hazards and recommend appropriate solutions to mitigate risks effectively. By hiring certified safety inspectors, organisations can rest assured that their safety feature assessments are conducted with the highest level of professionalism and accuracy.
Certified safety inspectors bring a wealth of knowledge and experience to safety feature assessments, providing valuable insights that can enhance the overall safety of a workplace. Their thorough evaluations can uncover hidden dangers that may have otherwise gone unnoticed, allowing employers to proactively address safety concerns and create a safer environment for employees. Investing in certified safety inspectors is an investment in the well-being of both employees and the business as a whole.
Frequency Recommendations for Safety Feature Assessments
Regular safety feature assessments are crucial to maintaining a safe work environment. The frequency of these assessments should be determined based on various factors such as the type of workplace, the nature of operations, and the level of risk involved. Generally, it is recommended to conduct safety feature assessments at least once a year to ensure that all safety systems are functioning optimally.
However, workplaces with higher risks or those that undergo frequent changes may require more frequent assessments. In such cases, a semi-annual or even quarterly assessment schedule may be necessary to address any potential issues in a timely manner. Regardless of the frequency, it is essential to establish a structured inspection plan and adhere to it diligently to uphold the safety standards of the workplace.
Determining the Ideal Inspection Schedule for Your Workplace
Determining the ideal inspection schedule for your workplace is crucial in maintaining a safe environment for employees and visitors. The frequency of safety feature assessments should be based on various factors such as the type of industry, the size of the workplace, and the specific safety features that need to be inspected regularly. It is recommended to consult with qualified safety inspectors to determine the most suitable inspection schedule for your particular workplace.
Regular safety feature assessments help in identifying potential hazards, ensuring that emergency systems are functional, and adhering to safety regulations. By establishing a consistent inspection schedule, you can proactively address any issues that may arise, mitigate risks, and create a culture of safety within the workplace. Remember, the safety and well-being of everyone in the workplace should be a top priority, making regular inspections an essential component of your safety management plan.
FAQS
How often should safety features be inspected in a workplace?
The frequency of safety feature inspections can vary depending on the type of equipment and workplace conditions. It is generally recommended to conduct inspections at least annually, but more frequent inspections may be necessary for high-risk environments.
Why is it important to hire certified safety inspectors for safety feature assessments?
Certified safety inspectors have the necessary training and expertise to identify potential safety hazards accurately. Hiring certified professionals ensures that safety assessments are thorough and compliant with industry standards.
What are some common issues that are typically identified during safety feature assessments?
Common issues identified during safety feature assessments may include faulty emergency lighting systems, malfunctioning fire alarms, expired fire extinguishers, inadequate signage, and blocked emergency exits.
How can faulty emergency lighting systems be addressed during safety inspections?
Faulty emergency lighting systems should be promptly repaired or replaced to ensure that they function effectively during emergencies. Regular testing and maintenance of emergency lighting systems are essential to address any issues proactively.
What is the role of qualified professionals in conducting safety inspections?
Qualified professionals play a crucial role in conducting safety inspections as they have the knowledge and skills to assess safety features accurately. Their expertise helps in identifying potential hazards and recommending appropriate corrective actions.
Related Links
How to Perform a Safety Sensor TestUnderstanding Garage Door Safety Mechanisms